Technology of Biomass Gasification
Biomass has been a major energy source, prior to the discovery of fossil fuels like coal and petroleum. Even though its role is presently diminished in developed countries, it is still widely used in rural communities of the developing countries for their energy needs in terms of cooking and limited industrial use. Biomass, besides using in solid form, can be converted into gaseous form through gasification route.
1. Concept and Principle
Gasification is the process of converting solid fuels to gaseous fuel. It is not simply pyrolysis; pyrolysis is only one of the steps in the conversion process. The other steps are combustion with air and reduction of the product of combustion, (water vapour and carbon dioxide) into combustible gases, (carbon monoxide, hydrogen, methane, some higher hydrocarbons) and inerts, (carbon dioxide and nitrogen). The process leads to a gas with some find dust and condensable compounds termed tar, both of which must be restricted to less than about 100 ppm each if the gas is to be used in internal combustion engines.
2. Uses of Producer Gas
The producer gas obtained by the process of gasification can have end use for thermal application or for mechanical/electrical power generation. Like any other gaseous fuel, producer gas has the control for power when compared to that of solid fuel, in this solid biomass. This also paves way for more efficient and cleaner operation. The producer gas can be conveniently used in number of applications as mentioned below.
2.1 Thermal
Thermal energy of the order of 5 MJ is released, by flaring 1 m3 of producer gas in the burner. Flame temperatures as high as 1550 K can be obtained by optimal pre-mixing of air with gas. For applications which require thermal energy, gasifiers can be a good option as a gas generator, and retrofitted with existing devices. Few of the devices to which gasifier could be retrofitted are
a) Dryers: Drying is the most essential process in beverage and spices industry like tea and cardamom. This calls for hot gases in the temperature range of 120 - 130 oC, in the existing designs. Typically the heat energy required is equivalent to 1 kg of wood for 1 kg made tea. Gasifier is an ideal solution for the above situation, where hot gas after combustion can be mixed with the right quantity of secondary air, so as to lower its temperature to the desired level for use in the existing dryers.
b) Kilns: Baking of tiles, potteries require hot environment in the temperature range of 800 - 950 oC. This is presently being done by combusting large quantities of wood in an inefficient manner. Gasifiers could be suitable for such applications, which provides a better option of regulating the thermal environment. There will also be an added advantage of smokeless and sootless operation, whereby enhancing the product value.
c) Furnaces: In non-ferrous metallurgical and foundry industries high temperatures (~650 - 1000 oC) are required for melting metals and alloys. This is commonly done by using expensive fuel oils or electrical heaters. Gasifiers are well suited for such applications.
d) Boilers: Process industries which require steam or hot water, use either biomass or coal as fuel in the boilers. Biomass is used inefficiently with higher pollutants like NOx and with little control with respect to power regulation. Therefore these devices are appropriate to be retrofitted with gasifiers for efficient energy usage.
Apart from these, energy requirements in poultry farms, cold storage devices (vapour compression refrigerator), rubber industry and so on could be met using wood gasifiers..
2.2 Power Generation
Using wood gas, it possible to operate a diesel engine on dual fuel mode. Diesel substitution of the order of 80 to 85% can be obtained at nominal loads. The mechanical energy thus derived can be used either for energising a water pump set for irrigational purpose or for coupling with an alternator for electrical power generation, either for local consumption or for grid synchronisation.
An appropriate oldwebcontent/site to realise the above application is an unelectrified village or hamlet. The benefits derived from this could be many, right from irrigation of fields to the supply of drinking water, and illuminating the village to supporting village industries. The other suitable oldwebcontent/sites could be saw mills and coffee plantations, where waste wood (of course of specified size) could be used as a feed stock in gasifiers.
3. Wood Gasifier
This system is meant for biomass having density in excess of 250 kg/m3. Theoretically, the ratio of air-to-fuel required for the complete combustion of the wood, defined as stoichiometric combustion is 6:1 to 6.5:1, with the end products being CO2 and H2O. Whereas, in gasification the combustion is carried at sub-stoichiometric conditions with air-to-fuel ratio being 1.5:1 to 1.8:1. The product gas thus generated during the gasification process is combustible. This process is made possible in a device called gasified, in a limited supply of air. A gasifier system (Fig. 1) basically comprises of a reactor where the gas is generated, and is followed by a cooling and cleaning train which cools and cleans the gas. The clean combustible gas is available for power generation in diesel-gen-set. Whereas, for thermal use the gas from the reactor can be directly fed to the combustor using an ejector.
4. Gasifier Specification
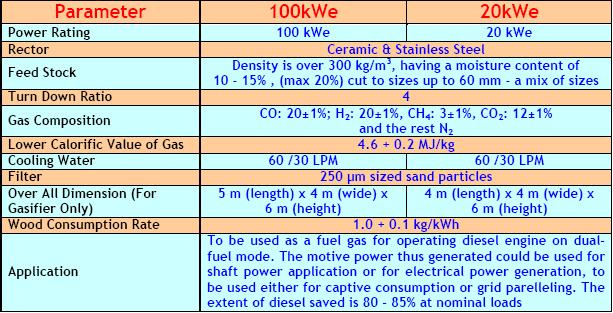
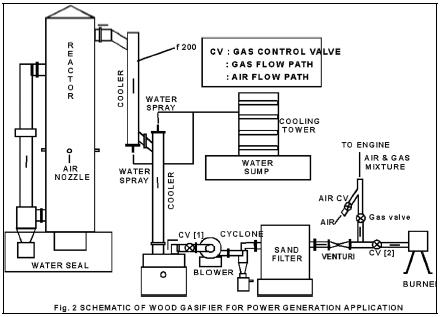